Partie 6 : montages à blanc et ajustages
Préparation du circuit d'huile:
Nous avons décidé d'installer un circuit full-flow. Cela veut dire que nous allons rajouter un filtre à huile à notre bloc type 1. Pour ce faire, il suffira de boucher la sortie de la pompe à huile et de récupérer l'huile à la sortie de la pompe en montant un couvercle pourvu d'une sortie. Le retour se fera juste après la sortie de la pompe à huile, dans la galerie principale.
Nous taraudons donc la sortie de notre pompe à huile avec un taraud 1/4 GAZ.
Nous vissons le bouchon 6 pans tête creuse...
...jusqu'à ce qu'il affleure à l'intérieur de la pompe.
Le bouchon sera monté avec de la loctite forte. Attention le filetage 1/4 GAZ est conique, donc il ne faut pas aller trop loin avec le taraud. Allez-y progressivement en vérifiant avec le bouchon pour voir ou vous en êtes.
Certains bouchent encore la galerie qui part de la pompe à huile pour plus de sécurité, mais c'est un peu inutile à nos yeux.
Nous allons maintenant préparer le retour de l'huile dans le bloc. Il suffit d'enlever la pastille qui obstrue la galerie principale, de percer avec un plus gros diamètre et de tarauder.
La photo suivante permet d'illustrer l'emplacement de cette pastille. Elle se trouve au milieu de la rondelle colorée en vert. La zone colorée en rouge est en fait la galerie d'huile allant de la pompe à huile à la galerie principale qui se trouve condamnée par le bouchon dans le corps de la pompe.
Nous perçons la pastille avec une mèche de 3mm, ce qui nous permettra d'y visser une vis Parker afin de la tirer dehors du bloc en utilisant des rondelles.
En superposant des rondelles et en vissant, nous finissons par sortir la pastille.
Nous perçons la galerie avec une mèche de 16,5 mm. Le diamètre est dicté par le filetage que vous avez sur la pièce qui fera le retour dans le bloc. Dans notre cas, il s'agit d'un filetage M18.
Nous allons ensuite éliminer la partie colorée en vert sur la photo précédente avec une fraise à lamer. Ca nous permet de gagner 5 précieux millimètres pour éviter que la pièce que nous allons y visser ne touche la tôle se situant derrière la poulie. Le lamage permet aussi de créer une portée pour que la rondelle en cuivre puisse étanchéifier notre raccord.
Il ne reste plus qu'à tarauder la galerie d'huile avec un taraud M18 x 1,5.
Il suffira encore de passer un petit coup de dremel sur la galerie parallèle afin de monter notre retour d'huile.
Le nouveau couvercle de pompe à huile a une sortie qui protège le circuit des surpressions grâce à un clapet qui s’ouvre et renvoi le surplus de pression avant les pignons.
Montage à blanc de la pompe à huile:
Comme nous sommes en train de bidouiller la pompe à huile, nous allons vérifier qu'elle ne touche pas l'aac une fois montée.
Le montage sur la photo n'est pas vraiment complet, il manque les vis de la taille droite, mais le vrai montage a démontré que les vis du pignon taille droite touchent un des axes de la pompe à huile, ici:
Nous allons diminuer cette partie d'un demi millimètre à la lime (ou à la fraiseuse, si vous en avez une)
Montage à blanc de l'arbre à cames:
Il est nécessaire de monter l'aac et les poussoirs pour vérifier qu'il y a assez de jeu entre ceux-ci. Il faut pouvoir passer une cale de 1 mm entre une came à la levée maximum et le poussoir. Comme nous avons un aac qui se monte avec des culbus décalés, nous sommes moins sujets à ce genre de problèmes. Si cela ne passe pas, il faudra soit usiner la tête des poussoirs, soit usiner le bloc pour réduire la longueur du logement, avec une nette préférence pour la deuxième solution.
Nous utilisons deux coussinets équipés de doubles épaulements. D’origine, il n’y a qu’un seul de ces coussinets sur un seul des demi blocs. On trouve facilement de ces kits dans le commerce aftermarket.
Préparation des poussoirs:
Nous allons juste relier les deux rigoles de lubrification pour nous assurer que l'huile les atteigne. C'est un truc Berg, qui dit que les trous de lubrification du bloc ne correspondent plus forcément avec les deux rigoles sur des poussoirs / blocs aftermarket. Cette petite opération nous permet de réduire le risque. Il suffit de faire une petite saignée d'un demi millimétre de profondeur avec une dremel
Montage des inserts:
Comme nos cylindres sont plus larges, nous allons monter des goujons de culasse en 8 mm. Donc hop!, perçage, filetage sur les 16 trous de goujons!.
Perçage en 10mm, la profondeur dépend bien évidemment de la longueur des inserts que vous utilisez:
Puis, taraudage en M12 x1,5. Il faut faire très attention en filetant le bloc, car l’alliage de magnésium est plutôt mou et c'est dommage de foirer un filetage une fois qu'il y a tout ce job de fait! En général, j'engage le taraud avec la perceuse à colonne pour être sur d'être bien droit et je finis avec un tourne à gauche.
Une fois que le bloc est prêt, il faut encore modifier les inserts pour être sur qu'ils ne vont pas dépasser le niveau du plan ou s'appuient les cylindres. Donc petite séance de montage-démontage-meulage pour assurer le coup.
Le nettoyage du filetage fraîchement créé permet d'assurer que la loctite tienne, car il faut monter les inserts et les goujons avec de la loctite forte.
Voici le résultat final.
Lamage pour les écrous M8 du bloc :
Il s’agit de créer une portée pour pouvoir monter des rondelles de culasses en 22mm. L’opération n’est pas très compliquée, il suffit d’utiliser une fraise à lamer et d’usiner chaque emplacement.
Equilibrage du vilo :
L’équilibrage dynamique est confié à une entreprise spécialisée. Nous allons juste essayer de citer les opérations nécessaires pour pouvoir être satisfait de son montage. Pour commencer, toutes les pièces en rotation sur l’axe du vilo doivent être équilibrées. Cela comprend donc le vilo, la poulie munie de son écrou, le volant moteur, également accompagné du boulon et le mécanisme d’embrayage sans disque.
Ensuite, il est important d’équilibrer chaque composant séparément avant l’équilibrage final qui se fera sur l’ensemble. Cela permettra par exemple de changer le mécanisme d’embrayage sans avoir à ouvrir le bloc pour rééquilibrer l’ensemble ou compromettre l’espérance de vie du bloc.
Les pièces achetées sont souvent déjà équilibrées, mais cela ne suffit pas. Une bonne entreprise équipée de matériel efficace pourra de toute façon faire mieux qu’une chaîne d’usinage chinoise.
Durant l’équilibrage, de la matière sera enlevée soit par meulage, soit par perçage.
Mise au poids des bielles :
Les bielles que nous utilisons sont révisées. Il ne nous reste qu’à les mettre au poids pour pouvoir les utiliser. La première opération sera donc de peser toutes les bielles et de trouver la plus légère. L’enlèvement de matière sur le pied de bielle et les supports de fixation du chapeau nous permettra de ramener l’ensemble des bielles à ce même poids au gramme près
On peut enlever de la matière sur les bielles d’origine où les flèches l’indiquent.
Nous avons également équilibré les pistons sur le même principe.
Rodage des culasses :
Pour garantir une étanchéité entre les cylindres et la culasse optimale, nous rodons chaque chemise avec son emplacement respectif sur la culasse. Il faut également prendre garde à repérer chaque piston et chemise pour les faire correspondre à la chambre de combustion avec laquelle ils ont été rodés. Ils ne sont dès lors plus interchangeables.
L’utilisation d’une pâte à roder de grain fin nous permet d’obtenir un plan de joint parfait. Nous en enduisons le sommet du cylindre comme sur l’image suivant ;
Le rodage s’effectue en mettant le cylindre dans sa position définitive et en effectuant des petites rotations de la chemise dans la culasse.
Voici un petit comparatif pour vous permettre d’apprécier les chambres de combustion avant et après rodage.
Il faut faire particulièrement attention à bien nettoyer la surface fraîchement rodée pour supprimer tous les résidus.
Dégagement du bloc pour la course longue :
Comme nous utilisons une course plus longue avec des bielles d’origine, nous allons devoir dégager passablement de matière pour permettre à l’ensemble mobile de fonctionner sans interférences.
Il n’y a pas de recette pour cette modification, il faut faire tourner l’ensemble et voir où se trouvent les problèmes. Comme il y a tout de même des endroits où l’enlèvement de matière est typique, nous allons montrer quelques photos.
Pour commencer, il faut dégager un passage pour les bielles sur le haut du bloc. Les premières opérations se font avec un demi bloc dans lequel on monte le vilo complet. Pendant que vouy êtes, marquez les coussinets, pour pouvoir les mettre directement à leur place lors du montage final.
Puis, il faut dégager les puits de cylindre à l’intérieur du bloc. Désolé pour la qualité des photos, les copeaux ont tendance à fausser la mise au point de l’appareil.
J’ai également légèrement fraisé le palier n° 2, mais cela résulte sûrement de mon montage. Le réglage du jeu axial permet d’ailleurs d’éviter de petit coup de dremel, mais la perte de rigidité est suffisamment faible comparé à la tolérance à la déformation gagnée.
Il faut ensuite fermer le bloc et refaire tourner le vilo pour vérifier où il touche encore le carter. C’est une opération qui prend du temps, mais la qualité du travail est absolument impérative.
Réglage du jeu axial :
Il s’agit de limiter le débattement axial du vilebrequin. Il se règle en variant l’épaisseur de 3 cales entre le volant moteur et le coussinet du palier voisin. Il ne faut pas diminuer le nombre de cale sous risque d’augmenter l’usure des cales. Elles ont aussi pour effet de diminuer la vitesse relative du volant moteur par rapport au coussinet, immobile.
Je fixe un comparateur sur mon support avec le palpeur perpendiculaire à la surface où se trouvera le disque d’embrayage. Il suffit ensuite d’effectuer un va et vient avec le vilo pour mesure le jeu actuel, qu’il faudra réduire à un dizième.
Une fois ce jeu mesuré, il faut disposer de cales de différentes épaisseurs pour arriver à régler ce jeu. Dans notre cas, j’avais mesuré 0,93mm de jeu, donc voici ce que je vais monter :
Mesure du deck height :
Nous devons aussi définir la distance entre le piston au point mort haut et le sommet de la chemise. Bien évidemment, nous avons décidé de cette valeur il y a des lustres, mais la mesure réelle nous permettra de définir la hauteur des cales que nous allons utiliser pour y arriver avec notre kit pistons / cylindres avec pistons hauts et notre course « longue ».
Il faut pouvoir serrer la chemise sur le bloc pour avoir une valeur réaliste. Le plus simple reste de disposer de l’outil spécifique.
Nous voulions avoir un deck height de 1,1mm, nous avons donc fait usiner des cales en inox de 3,1mm de haut, que l’on placera sous les cylindres pour les rehausser.
Géométrie de la distribution :
La première étape consiste à monter notre rampe de culbus décalés monté sur un axe rigide. Cela signifie simplement qu’à la place des rondelles ressort d’origine, nous allons utiliser des rondelles d’épaisseur et que les extrémités auront une rondelle vissée à la place du circlip d’origine.
Nous utilisons donc nos rondelles de différentes épaisseurs pour placer les culbuteurs en face des queues de soupape munis de leur capuchon.
Il faut arriver à ce résultat avant de poursuivre.
Nous allons désormais définir la longueur des tiges pour conserver au maximum le profil de notre aac. Pour ce faire, nous utilisons une tige réglable, dont nous pouvons faire varier la longueur avec un écrou.
Normalement le réglage s’effectue en regardant l’inclinaison de la vis de réglage par rapport à la queue de soupape, mais comme nos culbus décalés ont la vis de réglage du coté des tiges de culbu, notre réglage se fera en comparant l’angle entre la vis de réglage et la tige.
Il suffit de faire en sorte que l’angle entre les deux composants soit le même avec la soupape enfoncée que lorsque elle est au repos.
Pour arriver à ce résultat, nous avons du mettre des cales sous nos rampes.
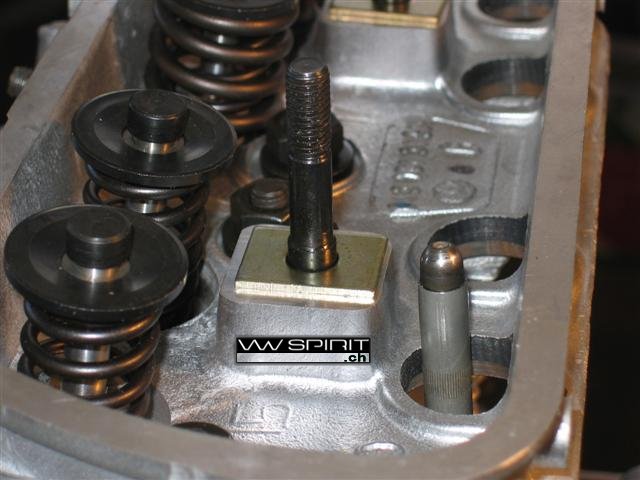 |